Reducing Production Waste With a Counting Scale
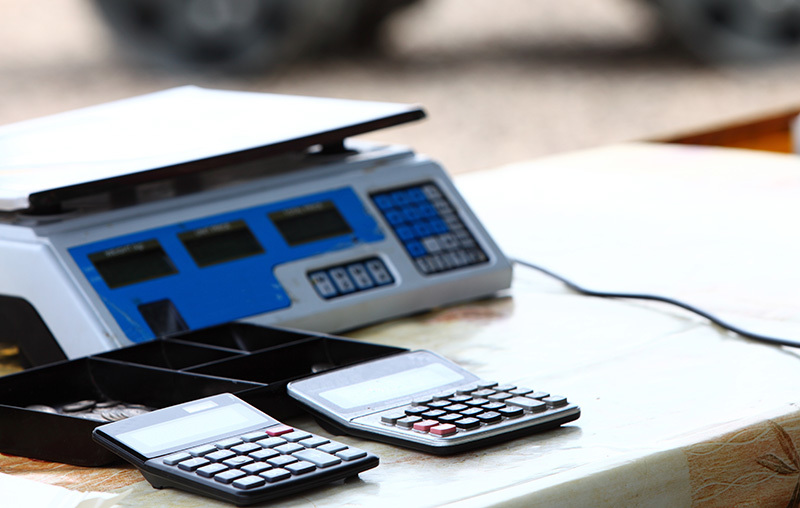
Production waste is an unwanted business cost - and one that could increase due to rising disposal costs, regulation and changes in customer demand. You can help to reduce the cost implications of production waste, as well as their environmental effects - by reading our new white paper. The guide explores the stages of production waste - and the benefits of lean production. It can be downloaded free below.
Counting scales are an effective monitoring tool and have been broadly implemented in waste reduction strategies within manufacturing industries and many more. In this post, we will share with you the various ways in which a counting scale can aid your business in keeping excess waste to a minimum.
Stages of production waste
When lean production originated in the Toyota Production System in Japan, they identified three general forms of waste - unproductive waste, inconsistent waste and unreasonable waste. From here, the stages at which production waste can be saved were identified.
1) Overproduction
Overproduction can occur when a business does not understand a customer's needs, which can lead to a business producing more products than required. Not only does this cause increased costs from needing more storage space, but you're also wasting resources that could be used for other products. The use of a counting scale at the end of the production process enables businesses to understand when it is time to stop producing.
2). Unnecessary transport
Needing to transport goods between factories or workshops is referred to as unnecessary transport because of the wasted fuel, energy and labour, as well as wear and tear. This is a result of multiple facilities, poor layouts and bad design. It can also result in damaged products. A counting scale can enable employees to effectively monitor the exact amount of the goods which you are transporting and ensure that unnecessary transportation is not occurring.
3) Inventory
Having too much inventory is also considered waste because of the cost of storing these items. This includes raw materials, goods that are in the process of being created and completed products. Seasonal changes, overproduction or excessive purchasing can cause inventory waste. By implementing a counting scale into your processes, it makes it easy for staff members to monitor large volumes of stock with ease. Use the P-NA with our JWI counting indicator for monitoring inventory.
4) Defects
If you're producing defects then you're wasting time, money, resources, and customer satisfaction. Causes for defect are poor design, poor machine repair, and lack of quality control. The use of a counting scale can ensure that businesses can make defects a thing of the past. With the close monitoring of a counting scale, you can ensure a high level of quality is consistency throughout your production process.
Choosing a counting scale
While counting scales cannot affect every stage of waste, it can help to improve certain stages, such as overproduction, inventory and waiting. Weighing scales - and in particularly counting scales - can be used to identify and therefore reduce business waste. In turn, making businesses more efficient.
When selecting a counting scale for your production processes, Marsden has a range of counting scales which can be tailored to what you are weighing. To give you more help we’ve put together this Buyers’ Guide, and this blog post with more helpful tips.
For highly precise parts counting, the Jadever JCE has graduations to 0.1g and has an internal counting resolution to 1/600,000.
Alternatively our JIK indicator can be used for weighing or counting. It has data transfer capabilities, so weight and count readings can be recorded on a spreadsheet throughout the production process. This further helps with inventory control, production control and compliance.
For more information about any of our counting scales, contact us here or call 01709 364296.